-
Raian IonescuMaterial quality very good. we have cooperate more than 10 Years. They trade lots kinds of steel material. All material quality good. They duty for all material quality. We are planing continue cooperate with them in the future
2205 Duplex Stainless Steel Plate High Strength Corrosion Resistance Alloy S32205 Plate
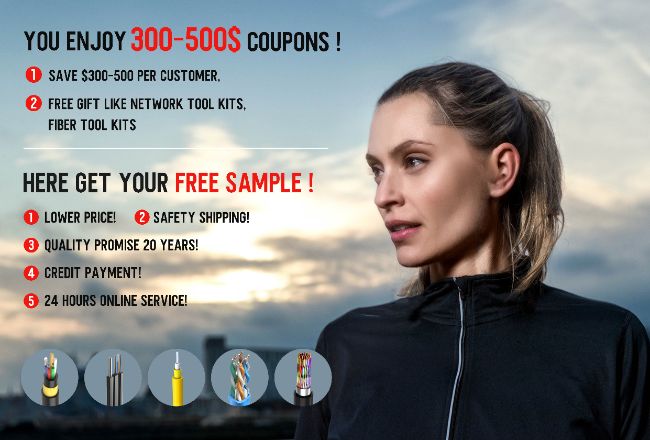
Contact me for free samples and coupons.
Whatsapp:0086 18588475571
Wechat: 0086 18588475571
Skype: sales10@aixton.com
If you have any concern, we provide 24-hour online help.
xProducts | Stainless Steel Plate | Grade | 2205 |
---|---|---|---|
Thickness | 3.0 - 80.0mm | Width | 1500mm 1800mm 2000mm |
Surface | NO.1 | Brand | BAOSTEEL TISCO |
Standard | ASTM A240/240M | Loading Port | Shanghai Port |
Highlight | S32205 Stainless Steel Plate,2205 Stainless Steel Plate,Corrosion Resistance Alloy Stainless Plate |
2205 Duplex Stainless Steel Plate High Strength Corrosion Resistance Alloy S32205 Plate
Products Specification
Products Name | 2205 Duplex Stainless Steel Plate |
Main Grades | Stainless Steel J1, J2, J4, 201, 202, 301, 304, 304H, 304L, 309, 309S, 310, 310S, 316, 316L, 316TI, 321, 321H, 347, 409, 410, 410S, 420, 430, 441, 904L,630,631,254SMO,253MA,2205,2507.etc |
Thickness | 3.0 - 80.0mm |
Width | 1250mm,1500mm ,1800mm,2000mm, or custom other size as request |
Length | 2000mm, 2440mm, 3000mm, 5800mm, 6000mm, AS PER CUSTOMER’S REQUIREMENT |
Type of Material | Laser Cutting |
Form | Plate / coil |
Test Certificate | Yes. |
Finish | NO.1, 2B, 2D, 2H, 2R, No.4, HAIRLINE, SCOTCH BRITE, SATIN FINISH, NO.8, BA. |
Brand | TISCO, LISCO,BAOSTEEL , POSCO, JISCO |
Product Information: 2205 Duplex Stainless Steel Plate
Material Grade: UNS S32205 / EN 1.4462 / F51 / F60
Overview:
2205 is a premium ferritic-austenitic (duplex) stainless steel characterized by an excellent combination of high strength and outstanding corrosion resistance. Its microstructure, comprising approximately 50% ferrite and 50% austenite, delivers superior performance compared to standard austenitic grades (like 304 or 316) in demanding environments.
Key Advantages:
-
Exceptional Strength: Delivers roughly twice the yield strength of standard austenitic stainless steels (304, 316), allowing for thinner sections, reduced weight, and potential cost savings.
-
Superior Corrosion Resistance: Offers excellent resistance to:
-
Stress Corrosion Cracking (SCC)
-
Pitting and Crevice Corrosion (high PREN >34: PREN = %Cr + 3.3x%Mo + 16x%N)
-
General corrosion in acids and chlorides
-
Corrosion fatigue and erosion corrosion
-
-
Good Weldability: Readily weldable using common techniques (recommended filler: 2209).
-
High Toughness & Ductility: Maintains good impact toughness down to low temperatures.
-
Favorable Thermal Conductivity & Low Thermal Expansion: Intermediate values between carbon steel and austenitic stainless steels.
Typical Chemical Composition (Weight %):
Element | Min | Max | Typical |
---|---|---|---|
Chromium (Cr) | 22.0 | 23.0 | 22.5 |
Nickel (Ni) | 4.5 | 6.5 | 5.7 |
Molybdenum (Mo) | 3.0 | 3.5 | 3.2 |
Manganese (Mn) | - | 2.0 | 1.2 |
Nitrogen (N) | 0.14 | 0.20 | 0.17 |
Silicon (Si) | - | 1.0 | 0.5 |
Carbon (C) | - | 0.030 | 0.015 |
Phosphorus (P) | - | 0.030 | 0.020 |
Sulfur (S) | - | 0.020 | 0.001 |
Iron (Fe) | Balance |
Typical Mechanical Properties (at Room Temperature):
Property | Value | Test Standard |
---|---|---|
0.2% Proof Strength | ≥ 450 MPa | ASTM A240 |
Tensile Strength | ≥ 620 MPa | ASTM A240 |
Elongation (50mm) | ≥ 25% | ASTM A240 |
Hardness (Brinell) | ≤ 290 HBW | ASTM E10 |
Hardness (Rockwell C) | ≤ 31 HRC | ASTM E18 |
Impact Toughness (Charpy V @ -46°C / -50°F) | ≥ 45 J (min avg.) | ASTM A923 Meth A |
Physical Properties:
-
Density: 7.8 g/cm³ (0.282 lb/in³)
-
Melting Range: 1380 - 1440 °C (2516 - 2624 °F)
-
Modulus of Elasticity: 200 GPa (29 x 10⁶ psi)
-
Thermal Expansion (20-100°C): 13.0 µm/m·°C (7.2 µin/in·°F)
-
Thermal Conductivity (20°C): 19 W/m·K (13.1 Btu·in/ft²·h·°F)
-
Electrical Resistivity: 0.80 µΩ·m
Available Forms & Sizes:
-
Thickness: Typically 0.5mm (0.020") up to 100mm (4") or more (subject to mill capability).
-
Width: Up to 3000mm (120") or wider (coil/plate).
-
Length: Standard mill lengths (e.g., 3000mm, 6000mm, 120") or custom cut-to-length.
-
Surface Finish: Standard Mill Finish (Hot Rolled Annealed & Pickled, or Cold Rolled Annealed & Pickled/Descaled), No. 1, 2B, BA, Polished (various grits), or as required.
Standards & Specifications:
-
ASTM A240/A240M (Pressure Vessels & General Application)
-
ASME SA-240
-
EN 10088-2
-
Other international equivalents available upon request.
Key Applications:
2205 duplex plate is ideal for demanding environments where high strength and corrosion resistance are critical:
-
Chemical & Petrochemical Processing: Pressure vessels, heat exchangers, reactors, piping, tanks (acids, chlorides).
-
Oil & Gas: Offshore platforms, downhole tubing, flowlines, separators, valves (sour service resistant).
-
Pulp & Paper: Digesters, bleach plants.
-
Desalination & Water Treatment: RO membranes, evaporators, piping.
-
Marine & Shipbuilding: Seawater piping, prop shafts, exhaust scrubbers.
-
Energy: Flue gas desulfurization (FGD) systems, geothermal plants.
-
Structural: Bridges, buildings in corrosive atmospheres.
-
Food & Pharmaceutical: High-pressure/high-temperature processing equipment.
Processing Considerations:
-
Cutting: Plasma, laser, waterjet, or mechanical methods are suitable. Avoid carbon steel contamination.
-
Forming: Requires higher forces than austenitic grades. Minimum bend radii are larger; consult forming guidelines.
-
Welding: Readily weldable using TIG, MIG, SAW, or Stick processes. Use matching duplex filler metal (e.g., ER2209 / E2209-xx). Control heat input and interpass temperature (typically max 150°C / 300°F) to maintain corrosion resistance and toughness. Post-weld heat treatment is generally not required for thin sections.
-
Machining: Tougher than austenitics; requires rigid setups, positive rake tools, adequate cooling, and lower speeds/higher feeds.
Why Choose 2205 Duplex Plate?
-
Cost Efficiency: Achieve the required strength and corrosion resistance with potentially less material thickness compared to 316L or 317L.
-
Long Service Life: Exceptional resistance to localized corrosion and SCC extends component lifespan in harsh conditions.
-
Design Flexibility: High strength enables lighter, more innovative designs.