-
Raian IonescuMaterial quality very good. we have cooperate more than 10 Years. They trade lots kinds of steel material. All material quality good. They duty for all material quality. We are planing continue cooperate with them in the future
High Purity 654SMO Stainless Steel Plate For Chemical Marine Power Generation Sectors
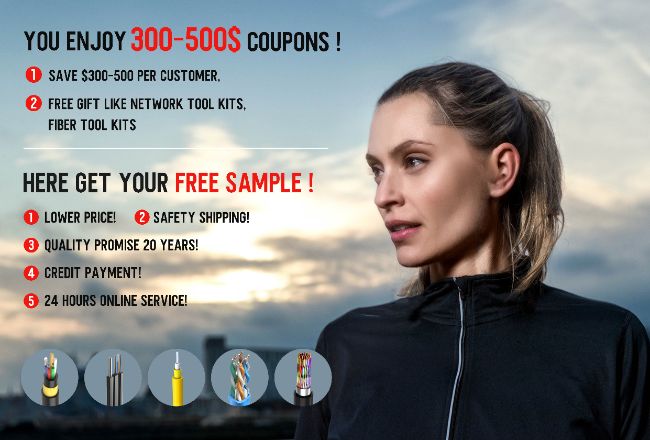
Contact me for free samples and coupons.
Whatsapp:0086 18588475571
Wechat: 0086 18588475571
Skype: sales10@aixton.com
If you have any concern, we provide 24-hour online help.
xProducts | Stainless Steel Plate | Grade | 654SMO |
---|---|---|---|
Thickness | 1.0 - 80.0mm | Width | 1500mm 1800mm 2000mm |
Surface | NO.1 | Brand | BAOSTEEL TISCO |
Standard | ASTM A240/240M | Loading Port | Shanghai Port |
Highlight | 654SMO Plate Marine,Power Generation Sectors 654SMO Plate,High Purity Stainless Steel Plate |
High Purity 654SMO Stainless Steel Plate For Chemical, Marine, Power Generation Sectors
Products Specification
Products Name | 654SMO Stainless Steel Plate |
Main Grades | Stainless Steel J1, J2, J4, 201, 202, 301, 304, 304H, 304L, 309, 309S, 310, 310S, 316, 316L, 316TI, 321, 321H, 347, 409, 410, 410S, 420, 430, 441, 904L,630,631,254SMO,654SMO,253MA,2205,2507.etc |
Thickness | 1.0 - 80.0mm |
Width | 1250mm,1500mm ,1800mm,2000mm, or custom other size as request |
Length | 2000mm, 2440mm, 3000mm, 5800mm, 6000mm, AS PER CUSTOMER’S REQUIREMENT |
Type of Material | Laser Cutting |
Form | Plate / coil |
Test Certificate | Yes. |
Finish | NO.1, 2B, 2D, 2H, 2R, No.4, HAIRLINE, SCOTCH BRITE, SATIN FINISH, NO.8, BA. |
Brand | TISCO, LISCO,BAOSTEEL , POSCO, JISCO |
654SMO Stainless Steel (UNS S32654)
654SMO is a super-austenitic stainless steel renowned for its exceptional corrosion resistance, particularly in extremely aggressive environments containing chlorides, acids, and other oxidizing media. It represents a significant advancement beyond standard austenitic grades (like 316L) and even duplex stainless steels in many demanding applications.
Key Characteristics & Composition:
-
High Alloy Content: Its outstanding properties stem from a carefully balanced high alloy composition:
-
High Chromium (Cr): ~24-25% - Provides excellent general corrosion resistance and oxidation resistance.
-
Very High Molybdenum (Mo): ~7.0-8.0% - Crucial for resistance to pitting and crevice corrosion, especially in chloride environments.
-
High Nitrogen (N): ~0.45-0.55% - Enhances pitting resistance, boosts strength, and stabilizes the austenitic structure.
-
Nickel (Ni): ~21-23% - Ensures a fully austenitic microstructure, providing toughness and ductility.
-
Manganese (Mn): ~3.0-4.0% - Aids in nitrogen solubility and contributes to strength.
-
Copper (Cu): ~0.30-0.60% - Improves resistance to sulfuric acid.
-
-
PREN Value: Its Pitting Resistance Equivalent Number (PREN = %Cr + 3.3x%Mo + 16x%N) is typically > 45, placing it among the highest corrosion-resistant stainless steels available. This quantifies its superior resistance to localized corrosion.
-
Outstanding Corrosion Resistance:
-
Pitting & Crevice Corrosion: Excels in seawater, brackish water, and high-chloride process streams where lower-alloyed steels fail.
-
Stress Corrosion Cracking (SCC): Highly resistant to chloride-induced SCC.
-
General Corrosion: Excellent resistance to a wide range of acids, including sulfuric, phosphoric, acetic, and formic acids, especially at moderate temperatures and concentrations.
-
-
High Strength: Significantly stronger than standard austenitic grades (e.g., 316L) due to nitrogen strengthening. Typical yield strength is around 450 MPa (65 ksi).
-
Good Ductility and Toughness: Maintains the good formability and impact toughness characteristic of austenitic structures.
-
Weldability: Generally weldable using standard techniques (TIG, MIG, SAW) but requires care (use of matching or over-alloyed filler metals like 625/825, low heat input control) to avoid issues like micro-segregation or sigma phase precipitation in the heat-affected zone (HAZ).
Typical Applications:
654SMO is used in critical components exposed to severe corrosion:
-
Chemical & Petrochemical Processing: Reactors, heat exchangers, piping, scrubbers, flue gas desulfurization (FGD) systems handling aggressive acids and chlorides.
-
Offshore & Marine: Seawater piping systems, pumps, valves, heat exchangers, shafting, fasteners in seawater environments.
-
Pulp & Paper Industry: Bleaching equipment, digesters.
-
Pollution Control: Scrubbers, waste gas treatment systems.
-
Pharmaceutical Industry: Equipment requiring high purity and corrosion resistance.
-
Flue Gas Cleaning.
-
Desalination Plants: Evaporator tubes, manifolds.
Advantages over Other Steels:
-
Superior to Standard Austenitics (304/316): Vastly better resistance to pitting, crevice corrosion, and SCC in chlorides and acids.
-
Superior to Duplex Steels (2205/2507): Higher resistance to uniform corrosion in many acids, better toughness/ductility at cryogenic temperatures, generally better weldability (less risk of detrimental phase formation). Often chosen where duplex steels approach their limits.
-
Cost-Effective Alternative to Nickel Alloys: While expensive compared to standard stainless, it often provides sufficient corrosion resistance at a lower cost than high-nickel alloys like Inconel 625, C-276, or Hastelloy in many applications.
Considerations:
-
High Cost: The high levels of alloying elements (Ni, Mo, N) make it significantly more expensive than standard stainless steels.
-
Fabrication: Requires more attention during machining, forming, and especially welding compared to lower-alloyed grades. Work hardening can occur during machining.
-
Thermal Stability: While stable, prolonged exposure in certain temperature ranges (e.g., 600-1000°C / 1110-1830°F) can lead to precipitation of secondary phases (like sigma, chi, Laves phases), potentially reducing corrosion resistance and toughness. Solution annealing is typically performed after hot working or welding to dissolve these phases.