-
Raian IonescuMaterial quality very good. we have cooperate more than 10 Years. They trade lots kinds of steel material. All material quality good. They duty for all material quality. We are planing continue cooperate with them in the future
AISI4140 Alloy Seamless Steel Pipe For Machining DN10 - DN400 SCH160 XXS
Place of Origin | China |
---|---|
Brand Name | DELTA |
Certification | ISO |
Model Number | Carbon Steel , Alloy Steel |
Minimum Order Quantity | 4 Tons |
Price | 610 - 820 USD/Ton |
Packaging Details | standard packing for export |
Delivery Time | 5 - 10 days based on the quantity |
Payment Terms | L/C, Western Union, T/T |
Supply Ability | 20Ton per week |
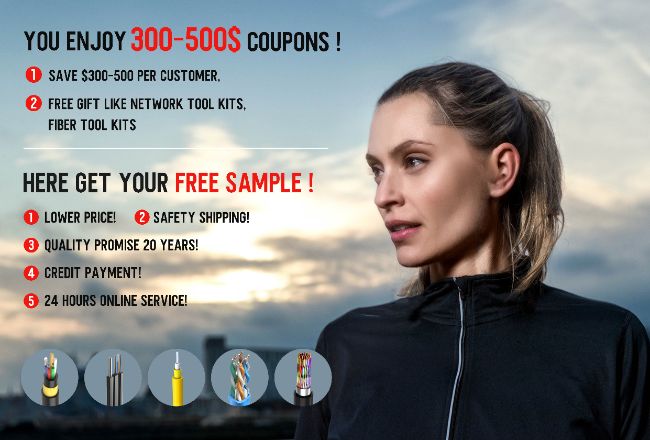
Contact me for free samples and coupons.
Whatsapp:0086 18588475571
Wechat: 0086 18588475571
Skype: sales10@aixton.com
If you have any concern, we provide 24-hour online help.
xProducts | Seamless Steel Pipe | Diameter | DN10 - DN600 |
---|---|---|---|
Thickness | 1.0 - 50.0mm | Length | 6-10m Or Cutting As Request |
Standard | ASTM EN GB DIN | Technique | Hot Rolled |
Service | Cutting Any Length As Request | MOQ | 2 Ton |
Highlight | machining Seamless Steel Pipe,DN10 DN400 Seamless Steel Pipe,SCH160 Seamless Steel Pipe |
AISI4140 Alloy Seamless Steel Pipe for machining DN10 - DN400 SCH160 XXS
Product name
|
SEAMLESS STEEL PIPE
|
Zinc Coating
|
custom
|
|
Material:
|
Carton steel/Alloy
|
Technique
|
hot rolled/cold drawn
|
|
Welding method
|
NO
|
Packing
|
Bare packing/Polyethylene sheet packing etc.
|
|
Standard
|
GB/T, ASTM, API, EN, DIN, JIS, etc.
|
Pipe Ends
|
Plain , Beveled , Coupling , Threading etc.
|
|
Grade
|
4130 4140 1045 1020 8620.etc
|
Surface Treatment
|
Galvanized , Painted , Epoxy Coated , 3PE Coated , etc.
|
|
Outer diameter
|
1/8 - 36 inch
( 10.3 - 914.4 mm) |
Product Application
|
Oil and Gas Delivery/Liquid Transport etc.
|
|
Wall thickness
|
25 - 50mm
|
Type
|
Fluid Pipe , Line pipe , Oil Casing , Alloy Pressure Pipe Low Temperature Pipe , Structural Pipe , etc.
|
|
Length
|
Random Length, SRL, DRL Fixed Length
|
Certifications
|
CE,ISO,SGS
|
|
delivery time
|
3-5days(in stock)
|
samples
|
YES
|
|
payment terms
|
TT
|
catelog
|
Please consult customer service to obtain
|
4140 steel is a versatile low-alloy steel that contains chromium, molybdenum, and manganese. Its composition imparts excellent hardenability, making it suitable for heat treatment processes. This steel alloy exhibits high tensile strength, good fatigue resistance, and exceptional toughness, making it ideal for applications that require durability and reliability.
4140 Steel Chemical Compositions
The chemical composition of 4140 steel typically includes the following elements:
- Carbon (C): 0.38-0.43%
- Chromium (Cr): 0.80-1.10%
- Manganese (Mn): 0.75-1.00%
- Silicon (Si): 0.15-0.35%
- Phosphorus (P): ≤0.035%
- Sulfur (S): ≤0.040%
- Molybdenum (Mo): 0.15-0.25%
Heat Treatment Methods
- Annealing: Annealing is the first step in the heat treatment process. It involves heating the steel to a specific temperature (around 800-850°C) and then slowly cooling it to room temperature. This process relieves internal stresses, refines the grain structure, and improves machinability.
- Normalizing: Normalizing is performed after annealing to further refine the microstructure. The steel is heated to a temperature slightly above the critical range (around 870-900°C) and then air-cooled. Normalizing enhances the steel’s strength and hardness while maintaining good ductility.
- Quenching: Quenching is a rapid cooling process that involves immersing the heated steel into a quenching medium, such as oil, water, or polymer. This step hardens the steel by transforming the austenite phase into martensite, a hard and brittle structure. The quenching process must be carefully controlled to prevent cracking or distortion.
- Tempering: Tempering is the final step in the heat treatment process. The quenched steel is reheated to a specific temperature (typically between 150-600°C) and then cooled in still air. Tempering reduces the brittleness of the steel, improves its toughness, and relieves residual stresses.