-
Raian IonescuMaterial quality very good. we have cooperate more than 10 Years. They trade lots kinds of steel material. All material quality good. They duty for all material quality. We are planing continue cooperate with them in the future
Cold Rolled Stainless Steel Strips Alloy 304/304L/304H SS Coils Slit Cutting Without Burr
Place of Origin | China |
---|---|
Brand Name | TISCO |
Certification | ISO |
Model Number | 300 Series / 400 Series |
Minimum Order Quantity | 2 Ton |
Price | 1500-2500 USD/Ton |
Packaging Details | standard packing for export |
Delivery Time | 5 - 12 days based on the quantity |
Payment Terms | L/C, T/T, Western Union |
Supply Ability | 20Ton per week |
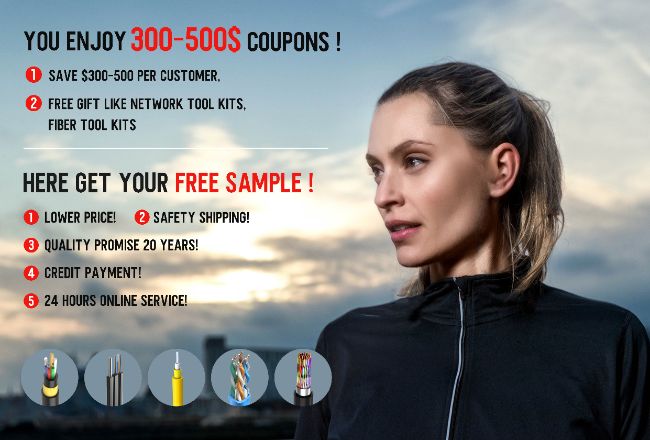
Contact me for free samples and coupons.
Whatsapp:0086 18588475571
Wechat: 0086 18588475571
Skype: sales10@aixton.com
If you have any concern, we provide 24-hour online help.
xProducts | Stainless Steel Strip | Thickness | 0.5-8.0mm |
---|---|---|---|
Width | Within 1500mm | MOQ | 500 Kgs |
Grade | 200 Series 300 Series 300 Series | Surface | BA 2B NO.4 HL 8K NO.1 |
Standard | ASTM EN GB JIS | Packing | Wooden Frame And Water Proof Paper |
Highlight | Cold Rolled Stainless Steel Strips,Slit Cutting Cold Rolled SS Strip,304L Cold Rolled SS Strip |
Cold Rolled Stainless Steel Strips Alloy 304/304L/304H SS Coils Slit Cutting Without Burr
Products Specification
Product Name | Stainless Steel Strips |
Length | As required |
Width | 3mm-1219mm or as required |
Thickness | 0.15 - 3.0mm or as required |
Standard | AISI,ASTM,DIN,JIS,GB,JIS,SUS,EN,etc. |
Technique | Hot rolled / cold rolled |
Surface Treatment | 2B or according to customer requirement |
Thickness tolerance | ±0.01mm |
Material | 201, 202, 301, 302, 303, 304, 304L, 304H, 310S, 316, 316L, 317L, 321,310S 309S, 410, 410S,420, 430, 431,434, 440A,904L,2205,2507 |
Application | It is widely used in high temperature applications, medical devices, building materials, chemistry, food industry, agriculture, ship components.It also applies to food, beverage packaging, kitchen supplies, trains, aircraft, conveyor belts, vehicles, bolts, nuts, springs, and screen. |
MOQ | 1tons.We also can accept sample order. |
Shipment time | Within 15-20 workdays after receiving deposit or L/C |
Export packing | Waterproof paper, and steel strip packed.Standard Export Seaworthy Package.Suit for all kinds of transport,or as required |
Capacity | 250,000 tons/year |
Stainless steel strips are essential materials in various industries due to their corrosion resistance, formability, and mechanical strength. Among the most widely used grades are 304, 304L, and 304H stainless steel strips, which belong to the austenitic 300-series family. While they share a common chemical base of chromium (Cr) and nickel (Ni), their distinct carbon content and resulting properties make them suitable for different applications. This guide explores their key differences, chemical compositions, mechanical properties, and real-world uses, helping you make an informed choice for your industrial needs.
What Are 304, 304L, and 304H Stainless Steel Strips?
These grades are part of the austenitic stainless steel category, characterized by a face-centered cubic crystal structure that provides excellent ductility and non-magnetic properties (in their annealed state). The primary differentiator among them is carbon content, which significantly impacts their:
- Corrosion resistance (especially in welded components)
- High-temperature strength and creep resistance
- Weldability and susceptibility to sensitization
- Mechanical properties like tensile strength and hardness
Key Differences: Chemical Composition
The table below outlines the ASTM-specified chemical compositions (by weight percentage) of the three grades:
Element
|
304 Stainless Steel Strip (ASTM A240/A240M) |
304L Stainless Steel Strip (ASTM A240/A240M) |
304H Stainless Steel Strip (ASTM A240/A240M) |
Carbon (C) |
≤ 0.08% |
≤ 0.03% |
0.04–0.10% |
Chromium (Cr) |
18.0–20.0% |
18.0–20.0% |
17.0–19.0% |
Nickel (Ni) |
8.0–10.5% |
8.0–12.0% |
9.0–12.0% |
Manganese (Mn) |
≤ 2.0% |
≤ 2.0% |
≤ 2.0% |
Silicon (Si) |
≤ 1.0% |
≤ 1.0% |
≤ 1.0% |
Phosphorus (P) |
≤ 0.045% |
≤ 0.045% |
≤ 0.045% |
Sulfur (S) |
≤ 0.030% |
≤ 0.030% |
≤ 0.030% |
Key Takeaways from Chemical Composition:
- Carbon Content: The most critical differentiator.
- 304L has ultra-low carbon (≤ 0.03%) to prevent sensitization during welding.
- 304H has higher carbon (0.04–0.10%) to enhance high-temperature strength.
- Chromium and Nickel: Provide passive film formation for corrosion resistance. All grades maintain similar Cr/Ni ratios, ensuring basic corrosion resistance, but 304L’s low carbon boosts resistance in welded joints.
Mechanical Properties Comparison
Below is a breakdown of their mechanical properties in the annealed condition:
Property |
304 |
304L |
304H |
Tensile Strength (MPa) |
≥ 515 |
≥ 485 |
≥ 515 |
Yield Strength (MPa) |
≥ 205 |
≥ 170 |
≥ 205 |
Elongation at Break (%) |
≥ 40 |
≥ 40 |
≥ 40 |
Hardness (HB) |
≤ 201 |
≤ 201 |
≤ 201 |
Density (g/cm³) |
7.93 |
7.93 |
7.93 |
Melting Point (°C) |
1398–1454 |
1398–1454 |
1398–1454 |
Key Observations:
- Strength: 304H offers slightly higher tensile and yield strength than 304L due to its higher carbon content, while 304 sits between the two.
- Ductility: All grades have excellent elongation (>40%), making them highly formable for stamping, rolling, or bending operations.
- High-Temperature Performance: 304H’s carbon content improves creep resistance at temperatures above 500°C, making it ideal for elevated-temperature applications.
Corrosion Resistance: How They Differ
All three grades exhibit excellent corrosion resistance in neutral or mildly corrosive environments (e.g., atmospheric exposure, water, or non-oxidizing acids). However, their performance varies in specific scenarios:
1. Welded Joints and Sensitization
- 304: Moderate resistance. High carbon (≤ 0.08%) can lead to chromium carbide precipitation (sensitization) at grain boundaries during welding, reducing corrosion resistance in the heat-affected zone (HAZ).
- 304L: Superior resistance. Low carbon (≤ 0.03%) minimizes carbide formation, making it "sensitization-resistant" without post-weld heat treatment. Critical for welded structures in corrosive environments.
- 304H: Similar to 304. Higher carbon increases sensitization risk, so post-weld heat treatment may be required for corrosion-sensitive applications.
2. Acid and Chloride Environments
- All grades struggle in strong chlorides (e.g., seawater) or concentrated acids (e.g., sulfuric acid). However, 304L’s low carbon provides marginally better resistance in welded components exposed to such media.
3. Oxidizing Atmospheres
- 304H shines here. Its higher carbon stabilizes the austenitic structure at high temperatures, maintaining strength in oxidizing environments like furnaces or boiler systems.
Weldability and Fabrication
Grade |
Weldability Notes |
Recommended Welding Processes |
304 |
Good weldability; preheat not required. Risk of sensitization in thick sections. |
TIG, MIG, spot welding, laser welding. |
304L |
Excellent weldability. Low carbon eliminates sensitization in HAZ. No post-weld heat treatment needed. |
Ideal for all welding processes, especially for thin sheets in corrosive service. |
304H |
Good weldability but higher carbon may require post-weld annealing for high-temperature applications. |
TIG/MIG with matching filler metal; ensure low-sulfur electrodes. |
High-Temperature Performance
When to Choose 304H?
- Service Temperature: 304H is designed for continuous use at 500–870°C, where its higher carbon content improves creep rupture strength and oxidation resistance.
- Applications: Furnace parts, heat exchangers, steam pipelines, and automotive exhaust systems that experience prolonged high temperatures.
Limitations of 304 and 304L at High Temperatures
- 304 is suitable up to 425°C for non-critical applications, while 304L’s low carbon reduces its high-temperature strength, making it less ideal for elevated-temperature service compared to 304H.
Common Applications by Grade
1. 304 Stainless Steel Strip
- Food and Beverage Industry: Conveyor belts, processing equipment, and storage tanks (due to non-toxicity and easy cleaning).
- Architecture: Decorative trims, facade panels, and roofing (weather resistance).
- General Manufacturing: Springs, brackets, and stamped components (excellent formability).
2. 304L Stainless Steel Strip
- Welded Structures: Chemical tanks, pharmaceutical reactors, and marine applications (where welded joints must resist corrosion).
- Medical Devices: Surgical instruments and implantable components (low carbon reduces corrosion risk in bodily fluids).
- High-Purity Systems: Semiconductor manufacturing and beverage bottling (minimal carbide formation ensures cleanliness).
3. 304H Stainless Steel Strip
- Power Generation: Boiler tubes, superheaters, and furnace liners (high-temperature strength).
- Automotive: Exhaust manifolds and catalytic converters (withstands thermal cycling).
- Aerospace: Non-critical high-temperature components (e.g., engine brackets in non-load-bearing roles).
How to Choose the Right Grade?
- Corrosion Environment:
- Mild environments: 304 is cost-effective.
- Welded components in corrosive media: 304L (no sensitization risk).
- Non-welded, high-temperature use: 304H.
- Temperature Requirements:
- Below 425°C: 304 or 304L (304L for welded parts).
- 425–870°C: 304H (prioritizes creep resistance).
- Fabrication Needs:
- Complex welding: 304L for hassle-free processing.
- High-temperature forming: 304H for retained strength during hot working.
- Cost Considerations:
- 304 is the most economical, 304L is slightly more expensive (due to low-carbon processing), and 304H is the priciest (specialized heat treatment required).
Keywords for Stainless Steel Strip Grades
Incorporate these keywords naturally for better search visibility:
- "304 stainless steel strip properties"
- "304L vs 304H stainless steel strip"
- "Stainless steel strip corrosion resistance"
- "High-temperature stainless steel strip 304H"
- "Weldable stainless steel strip 304L"
- "304 stainless steel strip applications"