All Products
-
Raian IonescuMaterial quality very good. we have cooperate more than 10 Years. They trade lots kinds of steel material. All material quality good. They duty for all material quality. We are planing continue cooperate with them in the future
NO.1 Surface 2205 Duplex Stainless Steel Plate For Chemical Processing And Marine 3.0 80.0mm Thickness
Place of Origin | China |
---|---|
Brand Name | TISCO BAOSTEEL |
Certification | ISO |
Model Number | 2205 / 1.4462 |
Minimum Order Quantity | 500 kgs |
Price | 1800 - 3200 USD/Ton |
Packaging Details | standard packing for export |
Delivery Time | 5 - 12 days based on the quantity |
Payment Terms | T/T, Western Union |
Supply Ability | 20Ton per week |
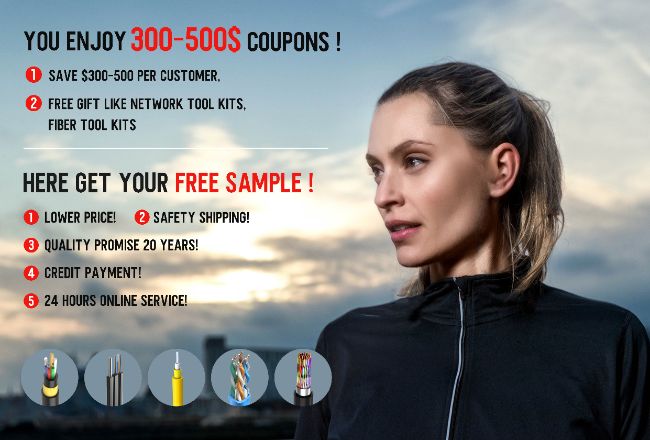
Contact me for free samples and coupons.
Whatsapp:0086 18588475571
Wechat: 0086 18588475571
Skype: sales10@aixton.com
If you have any concern, we provide 24-hour online help.
xProduct Details
Products | Stainless Steel Plate | Grade | 2205 / 1.4462 |
---|---|---|---|
Thickness | 3.0 - 80.0mm | Width | 1500mm 1800mm 2000mm |
Surface | NO.1 | Brand | BAOSTEEL TISCO |
Standard | ASTM A240/240M | Loading Port | Shanghai Port |
Highlight | 3.0 80.0mm Thick Stainless Steel Plate,2205 Duplex Stainless Steel Plate,Chemical Processing Stainless Steel Plate |
Product Description
2205 Duplex Stainless Steel Plate for Chemical Processing Marine Use
Products Specification
Products Name | 2205 Duplex Stainless Steel Plate |
Main Grades | Stainless Steel J1, J2, J4, 201, 202, 301, 304, 304H, 304L, 309, 309S, 310, 310S, 316, 316L, 316TI, 321, 321H, 347, 409, 410, 410S, 420, 430, 441, 904L,630,631,254SMO,253MA,2205,2507.etc |
Thickness | 3.0 - 80.0mm |
Width | 1250mm,1500mm ,1800mm,2000mm, or custom other size as request |
Length | 2000mm, 2440mm, 3000mm, 5800mm, 6000mm, AS PER CUSTOMER’S REQUIREMENT |
Type of Material | Laser Cutting |
Form | Plate / coil |
Test Certificate | Yes. |
Finish | NO.1, 2B, 2D, 2H, 2R, No.4, HAIRLINE, SCOTCH BRITE, SATIN FINISH, NO.8, BA. |
Brand | TISCO, LISCO,BAOSTEEL , POSCO, JISCO |
2205 Duplex Stainless Steel: Engineering Excellence in Corrosion Resistance
Alloy Composition: Precision in Engineering
Mechanical Attributes: Strength Without Compromise
Corrosion Resistance: Mastering Hostile Environments
Fabrication Nuances: Crafting with Precision
Industry Applications: Where Failure is Not an Option
Global Standards and Comparative Edge
Recommended Products